Corn stover refers to stalks, leaves and cobs that remain in fields after the corn harvest. This biomass can be used in producing ethanol. Corn stover is the primary biomass source being used for producing cellulosic ethanol in the United States (Wilhelm et al. 2007).
Research indicates that farmers can harvest stover for cellulosic sugars that can be fermented into ethanol. Concerns about carbon dioxide emissions and global warming have prompted renewed interest in using corn stover for energy production. Lack of markets, concerns about sustained soil productivity and lack of commercial conversion technologies had precluded the widespread harvest of corn residues for this purpose until recently (Mann et al. 2002).
Corn stover could supply as much as 25 percent of the biofuel crop needed by 2030. The corn stover ethanol byproduct has three times the concentration of nitrogen as the original cornstalks (Wilhelm et al. 2007).

Corn stover is the largest quantity of biomass residue in the United States. Around 120 million tons of biomass residue is available annually. This stover has the potential of supplying 23 to 53 billion liters of fuel ethanol to the U.S. transportation market, up to 10 percent of total gasoline needs.
Until the 1996-1997 crop year, there was little experience collecting corn stover on a large scale. The large stalk makes it different from baling other stover. Corn stover could also be used for other purposes such as for animal bedding. Its fiber content helps in making paper, but economics remain a hurdle (Glassner et al. 1998).
Corn stover is composed of about 70 percent cellulose and hemicellulose, and 15 to 20 percent lignin. Cellulose and hemicellulose can be converted to ethanol, and lignin burned as a boiler fuel for steam/electricity generation.
Developing ways to quickly collect, handle and store biomass economically is required for biomass-to-ethanol commercialization, along with improved process technology. Theoretically speaking, according to scientists, around 130 gallons of ethanol could be produced per ton of corn stover (Glassner et al. 1998).
In 1970s and early 1980s, interest in U.S. energy self-sufficiency prompted research on the potential of using farm crop residues for energy production. It was thought that residues, including unharvested leafy stalks, could be used for energy production, either through direct combustion of residues or through microbial conversion of residues to ethanol fuel.
Technologies to convert corn residues to ethanol fuels have been developed only recently, during the past decade.
If concerns about environmental sustainability, especially soil quality, are understood and appropriate measures to ensure sustainable harvest can be implemented, corn stover may provide an additional, significant source of corn-based renewable fuels (Mann et al. 2002).
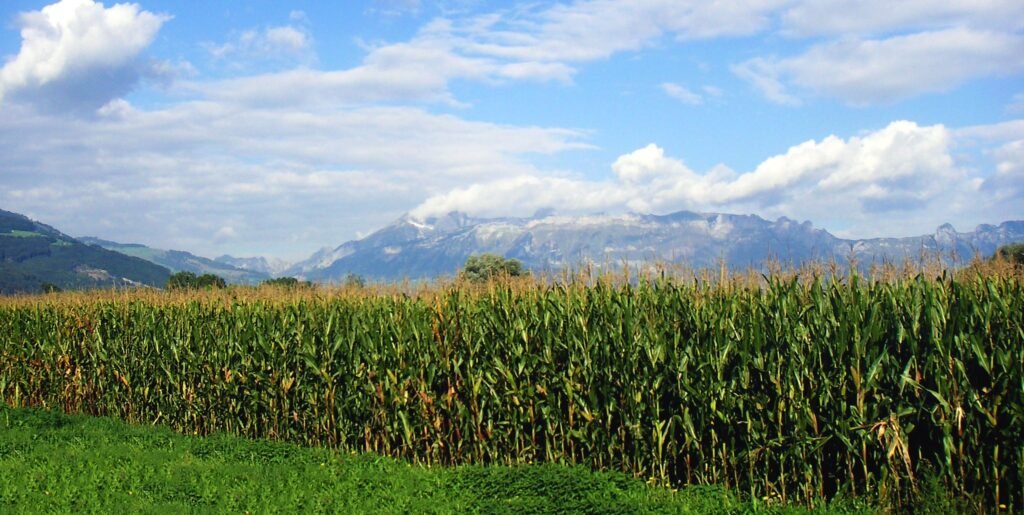
The two important routes to converting corn stover into biofuels are: biological conversion and thermochemical conversion. Biological conversion involves four steps: pretreatment, enzymatic saccharification, fermentation and recovery.
The thermochemical conversion involves gasification and pyrolysis. Pyrolysis oil (bio-oil) is produced when corn stover is rapidly heated in the absence of air to temperatures ranging from 400 to 600 degrees C. Bio-oil is composed of hydrocarbons, gases and charcoal.
Bio-oil can be refined into biofuel (Agriculture and Agri-Food Canada 2008). In gasification, the stover is gasified and carbon monoxide, hydrogen and carbon dioxide in the synthesis gas are fermented into ethanol.
The interest in corn stover primarily centered on highly productive corn lands where erosion control might not require leaving all of the corn stover in the field. Researchers are concerned that removing corn stover to produce ethanol may have adverse effects on soil erosion, soil organic carbon (SOC), pests, pesticides, diseases and stand establishment.
Nutrient supply, and nitrate and pesticide leaching are also a matter of concern related to no-till continuous corn. Most research discussions acknowledge potential tradeoffs among beneficial and adverse effects (Mann et al. 2002).
The mass of stover needed to keep soil loss from water and wind erosion less than a tolerable limit were estimated for soils in selected counties in the U.S. Corn Belt. It was found that excess stover, the amount remaining after these environmental concerns were addressed, could be removed for other uses (Johnson et al. as cited in Wilhelm et al. 2007).
Harvestable stover at various corn grain yield levels limited by the need to sustain SOC were calculated, and these estimates assumed a harvest index of 0.53 [mass of grain/(mass of grain + mass of stover)] for corn (Johnson et al. 2006 as cited in Wilhelm et al. 2007).
Harvestable stover varies widely with cropping practice. Even after considering SOC dynamics, stover needed to maintain SOC was greater than that required to control erosion. More research at additional field sites is required to generate truly sustainable biomass feedstock production and harvest guidelines (Wilhelm et al. 2007).
But, the research conducted thus far indicates the advantages of harvesting stover for ethanol production after considering environmental factors.
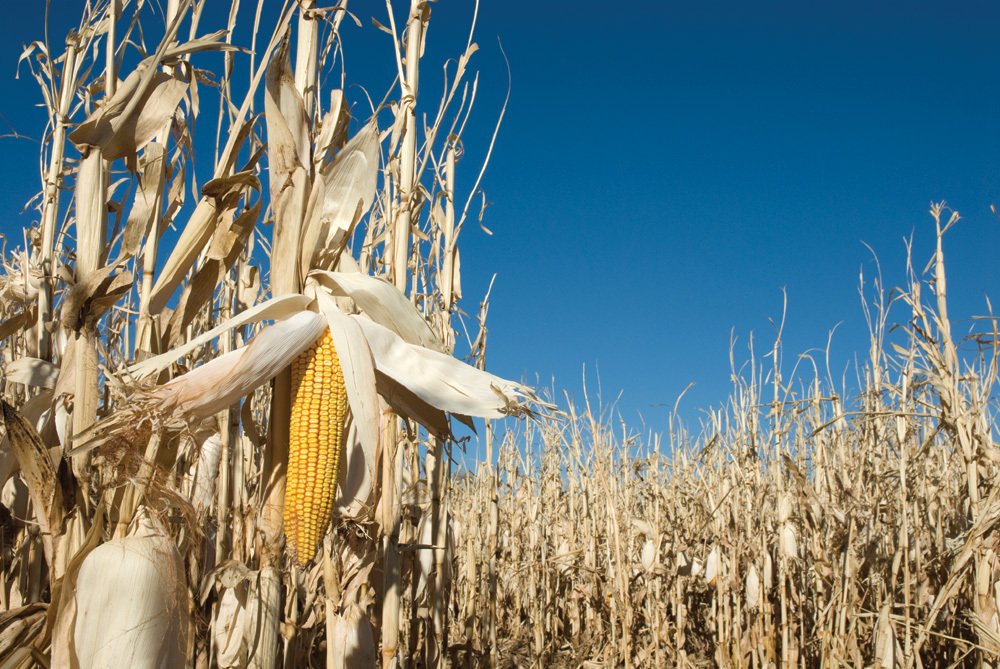
It is estimated that about 1 kilogram of stover is produced per kilogram of corn grain (Glassner et al. 1999). U.S. corn production in 2008 was 12.1 billion bushels, down from 13.1 billion bushels in 2007. The yield was 153.8 bushels per acre. U.S. planted area under corn was 85.9 million acres (NASS 2008).
Under the current corn production practices, less than 28 percent of the stover produced in the United States could be sustainably collected at a farmgate cost of less than $33.07 per Mg ($30 per dry ton).
More stringent soil loss constraints would lower this value considerably. However, if farmers chose to universally convert to no-till corn management and total stover production did not change, the sustainable supply would almost double.
Given current (1997–2000 average) U.S. corn production, 91.8 to 106.1 million Mg (105-117 million dry tons) of stover would be potentially collectable if farmers managed their cornfields to produce harvestable grain and stover (Graham et al. 2007).
Wind erosion is a major constraint to stover collection. Research suggests that central Illinois, northern Iowa, southern Minnesota and the Platte River region in Nebraska produce sufficient stover to support large biorefineries with one million Mg per year feedstock demands and that if farmers converted to universal no-till production of corn, then over 100 million Mg of stover could be collected annually without causing erosion to exceed the tolerable soil loss (Graham et al. 2007).
The height at which corn has to be harvested to ensure the most economical and efficient stover harvest is an important factor in ethanol production. Research indicates that a normal-cut harvest results in the most economical and efficient stover harvest for biofuel production.
At least 16 inches of stubble should remain on the field for it to be considered normal-cut stover harvest (Perry 2008).
A study published by the Center for Agricultural and Rural Development (CARD) at Iowa State University in 2007 concluded that cellulosic ethanol using corn stover will not be feasible in the Corn Belt and would require a break-even corn price of $4.80 per bushel (Neeley 2008).
There is still some discussion and uncertainty on using corn stover for ethanol production as it may affect soil and water erosion and other beneficial effects stover could have if left in the field. But, there is sufficient research that indicates that stover could be harvested for ethanol production even after considering the other environmental factors. More research is needed and is being conducted about this issue.