Selecting the right pet food extruder machine is a critical decision for manufacturers aiming to produce high-quality pet food products while maintaining efficiency and cost-effectiveness. Given the growing demand for diverse pet food products, the choice of an extruder can significantly impact production capabilities and product quality. Here’s a comprehensive guide to help you choose the right pet food extruder machine:
1. Production Capacity
- Small-scale production (50-200 kg/hour): Ideal for small businesses or pilot projects.
- Medium-scale production (500-1000 kg/hour): Suitable for growing businesses or medium-sized manufacturers.
- Large-scale production (1-5 tons/hour): Designed for large commercial operations.
Ensure that the machine’s capacity matches your current production needs and allows room for future expansion.
2. Types of Pet Food Products
- Dry Kibble
- Semi-Moist Food
- Treats and Biscuits
- Specialty Diets (e.g., Grain-Free, High-Protein)
Different pet food types may require specific extrusion capabilities, so choose a machine that can accommodate your desired product range.
3. Extruder Configuration
- Single-Screw Extruders: More affordable, suitable for simpler formulations.
- Twin-Screw Extruders: Offers greater versatility and control, ideal for complex recipes and specialty products.
Choose the extruder configuration based on the complexity of your products and your innovation plans.
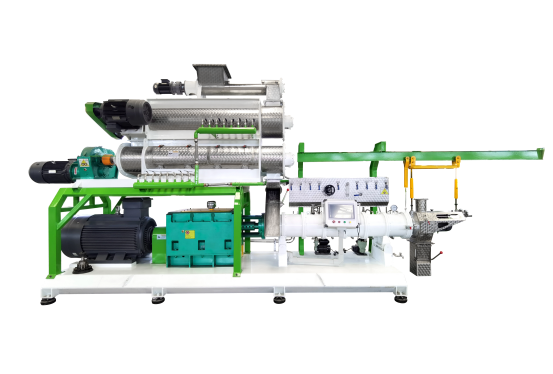
4. Temperature Control and Cooking Capabilities
- Look for machines with precise temperature control.
- Consider extruders with multiple heating zones for better process control.
- Check for steam injection capabilities for improved cooking and gelatinization.
Ensure the extruder can meet the necessary cooking temperatures and times for your specific formulations.
5. Die and Cutter System
- Interchangeable Dies: For variety in product shapes and sizes.
- Adjustable Cutters: For producing different kibble sizes.
- Durability of Materials: Ensure the system’s components are durable and long-lasting.
A flexible die and cutter system allows for greater product variety.
6. Material Construction and Durability
- Prefer food-grade stainless steel construction.
- Opt for wear-resistant materials in high-stress areas.
- Consider corrosion-resistant coatings for longevity.
A durable machine will reduce maintenance costs and have a longer lifespan.
7. Ease of Cleaning and Maintenance
- Look for machines with easy-to-disassemble components.
- Consider extruders with CIP (Clean-in-Place) systems.
- Ensure accessibility of all parts for thorough cleaning.
Efficient cleaning and maintenance are essential for food safety and reducing downtime.
8. Energy Efficiency
- Choose machines with high energy efficiency ratings.
- Consider models with variable speed drives to optimize energy use.
- Check if the machine has energy recovery systems.
An energy-efficient extruder can reduce operational costs, especially for large-scale production.
9. Control Systems and Automation
- PLC Systems: For precise process control.
- Touch Screen Interfaces: For user-friendly operation.
- Recipe Management: For consistent production.
- Data Logging and Reporting: For quality control.
Advanced control systems enhance product consistency and ease of operation.
10. Flexibility and Scalability
- Look for extruders that can handle a wide range of ingredients.
- Check if the machine can be easily upgraded or expanded.
- Consider modular systems that allow for future additions.
A flexible and scalable extruder will adapt to your changing business needs.
11. Brand Reputation and After-Sales Support
- Research customer reviews and testimonials.
- Check the manufacturer’s history and experience in pet food extrusion.
- Ensure availability of spare parts and technical support.
- Look for warranties and service agreements.
Reliable after-sales support is crucial for maintaining your machine and minimizing downtime.
12. Compliance with Food Safety Standards
- Ensure the extruder complies with FDA regulations for pet food production.
- Check for HACCP (Hazard Analysis and Critical Control Points) compatibility.
- Consider features that support FSMA (Food Safety Modernization Act) compliance.
Compliance with food safety standards is essential for legal operation and market acceptance.
13. Cost and Return on Investment (ROI)
- Evaluate the initial purchase price, installation costs, operating costs, and expected lifespan.
- Calculate the potential revenue from increased production capabilities.
- Consider the ROI to ensure the machine aligns with your business goals.
Balance the initial investment with long-term benefits and operational efficiency.
14. Integration with Existing Equipment
- Check compatibility with existing pre- and post-extrusion equipment.
- Consider space requirements and facility layout.
- Evaluate any necessary upgrades to supporting systems (e.g., power supply, cooling systems).
Seamless integration with your existing setup will minimize disruptions during installation.
Conclusion
Selecting the right pet food extruder machine requires careful consideration of your production needs, product types, and operational goals. By evaluating these factors, you can choose a machine that meets your current requirements and supports future growth. Investing in a high-quality, versatile extruder will enable you to produce consistent, high-quality pet food products, positioning your business for success in the competitive pet food industry.