The ring die pellet machine is a sophisticated piece of processing equipment designed to efficiently convert a wide array of raw materials into high-density pellets. This machine uses a ring-shaped die to compress materials such as animal feed, biomass, and various waste products, transforming them into uniform pellets.
This pelleting process is crucial for industries like agriculture, biofuels, and recycling, providing a sustainable and efficient solution for material handling and utilization.
Primarily, the ring die pellet machine is known for its ability to handle different feedstocks and convert them into compact, energy-dense pellets. This not only optimizes storage and transportation but also enhances the usability of the raw materials.
For instance, in the agricultural sector, it is extensively used to produce feed pellets, improving feed quality and nutritional uniformity for livestock. In the biofuels industry, converting biomass into pellets presents a renewable energy source that supports environmental sustainability.
Moreover, the recycling industry benefits significantly from the ring die pellet mill’s capability to process waste materials, reducing landfill requirements and promoting material recovery. By pelleting these materials, industries can more effectively manage waste and contribute to a circular economy. The efficiency of the ring die pellet machine lies in its continuous operation and high-capacity output, making it a valuable asset for large-scale operations.
Its widespread popularity in various sectors underscores the versatility and reliability of the ring die pellet machine. This equipment is designed for durability and ease of maintenance, ensuring consistent performance over extended periods.
Additionally, advancements in technology have made these machines more accessible, with user-friendly control systems and customizable die configurations to meet specific pelleting needs.
2. Benefits of a Ring Die Pellet Mill
1. Higher Efficiency: One of the foremost advantages of the ring die pellet machine lies in its superior efficiency. Compared to flat die machines, ring die pellet mills leverage a more complex and sophisticated feeding mechanism, which ensures a continuous and smooth operation.
This not only minimizes downtime but also maximizes the throughput, leading to a significantly enhanced production rate.The ring die equipment can handle larger volumes, making it an ideal choice for industrial-scale pellet production.
2. Consistent Pellet Quality: Producing uniform, high-quality pellets is paramount for industries reliant on these tiny, compressed fuel sources. The ring die pellet mill stands out because of its ability to generate pellets with consistent size, density, and moisture content.
The design of the ring die ensures an even distribution of material during operation, resulting in pellets that meet stringent quality standards and uniformity, which is crucial for efficient combustion or feeding processes.
3. Durability: The robust construction of ring die pellet machines ensures they can withstand the rigors of continuous, heavy-duty operation. Made from high-quality, wear-resistant materials, the components of these machines, including the die and roller, are designed for longevity.
This durability reduces the frequency of maintenance and part replacement, resulting in lower operational costs and minimal downtime, enhancing the overall productivity.
4. Lower Energy Consumption: Despite their powerful performance, ring die pellet mills are engineered to be energy-efficient. Their design optimizes the usage of power, ensuring that less energy is wasted during operation. This efficiency translates into reduced operational costs, making the ring die pellet machine an economically favorable option for long-term use.
5. Versatility: Another significant benefit of the ring die pellet machine is its versatility. These machines are capable of processing a wide range of materials, including various types of biomass like wood, straw, and agricultural residues. This adaptability makes them suitable for diverse applications across different industries, further underscoring their utility and value.
Why Choose a Ring Die Pellet Mill?
The ring die pellet mill offers numerous advantages that make it a preferred option for many industries. Below, we delve into the key benefits that underscore the suitability of this advanced machinery.
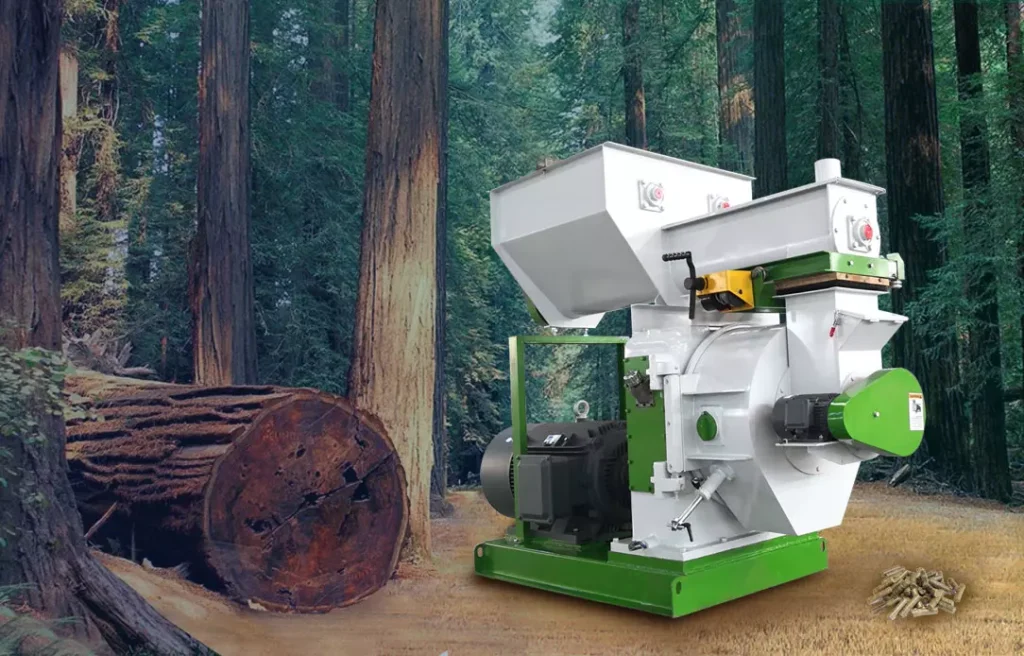
1. Enhanced Output
A prominent advantage of the ring die pellet machine is its ability to deliver higher output rates. The ring die design enables continuous operation at full capacity, which significantly boosts productivity. The larger surface area means more raw material can be processed per unit of time, enhancing overall efficiency and throughput.
2. Reduced Maintenance
Another benefit of the ring die pellet mill is its reduced maintenance requirement. Due to its robust construction and superior engineering, the machine experiences less wear and tear, enabling it to function for extended periods without the need for frequent repairs. This lowers downtime and allows for more consistent production cycles, which is vital for maintaining operational efficiency.
3. Cost-Effectiveness
While the initial investment for a ring die pellet machine may be higher than alternative options, it proves to be cost-effective in the long run. The enhanced output and reduced maintenance translate to lower overall operational costs. Moreover, the durability of the machine means that it has a longer lifespan, providing better returns on investment over time.
4. Precision Engineering
The precision engineering of the ring die pellet mill ensures high efficiency in the pelletizing process. Advanced technology and meticulous design allow for uniform pellet size and density, which is crucial for many applications where consistency is key. This precision not only improves product quality but also reduces material wastage.
5. Environmental Benefits
Opting for a ring die pellet machine also brings environmental advantages. These machines are designed to operate with lower emissions, contributing to a reduction in the carbon footprint. Additionally, the efficient pelletizing process minimizes wastage, ensuring that resources are used judiciously and sustainably.
Choosing a ring die pellet machine is, therefore, a strategic decision that reaps multiple benefits, from enhanced productivity and cost savings to precision and environmental sustainability.
4. Working Principle of a Ring Die Pellet Machine
A ring die pellet machine, alternatively known as a ring die pellet mill, follows a systematic process to convert raw materials into high-quality pellets. This process can be broken down into the following stages:
1. Material Feeding: The process begins with material feeding. Raw materials, which can include various types of biomass like wood chips, sawdust, or agricultural residues, are fed into the machine via a hopper. The uniform and consistent flow of materials into the pellet chamber is crucial for maintaining efficiency and pellet quality.
2. Conditioning: Once the materials are within the pellet mill, they undergo a conditioning process. During this phase, the materials are mixed and moistened to achieve the optimal moisture and temperature conditions. This step is essential as it softens the raw materials and prepares them for better compression into pellets.
3. Pelleting: The conditioned materials are then pressed through the ring die and rollers. The ring die, a circular structure with multiple holes, ensures uniform pellet formation. The rollers rotate to push the material through these die holes, compressing the fibers and forming the cylindrical pellets. Precision in this stage ensures pellets are densely packed, which is critical for their durability and energy efficiency.
4. Cooling: After emerging from the die, the freshly formed pellets are hot and somewhat pliable. They are subsequently directed to a cooling system. The cooling process stabilizes the pellets, reducing their temperature and moisture content, which solidifies their structure and prevents them from crumbling. Proper cooling ensures that the final product is both stable and of high quality, ready for packaging and use.
By following these stages meticulously, a ring die pellet mill ensures the production of consistent, high-quality pellets suitable for various applications, from heating solutions to animal feed.
Specific Parameters of a Ring Die Pellet Mill
When selecting an appropriate ring die pellet mill, understanding its specific parameters is crucial for optimizing performance and ensuring the machine meets your operational needs. Here, we will outline some critical specifications that should be carefully considered.
1. Die Diameter: The die diameter significantly influences the production efficiency and pellet quality. Typical ranges for die diameters in ring die pellet mills span from 250 mm to 900 mm. A larger die diameter generally allows for higher throughput and improved pellet density, making it essential to match the die size with the production scale and type of material being processed.
2. Capacity: The capacity of a ring die pellet mill is indicative of the quantity of output it can produce within a specific timeframe. This can vary widely based on the model and type of the machine. On average, capacities can range from 1 ton per hour to over 15 tons per hour. Selecting a machine with the appropriate capacity ensures effective resource utilization and meets production targets efficiently.
3. Motor Power: The motor power is a pivotal factor in determining the pellet mill’s performance. It is typically measured in kilowatts (kW) and can range from 55 kW to more than 300 kW. Adequate motor power not only ensures the facilitation of continuous operation but also impacts the overall durability and maintenance needs of the machine. Therefore, aligning the motor power with production requirements is imperative for smooth production processes.
4. Pellet Size: Ring die pellet mills have the capacity to produce pellets in a variety of sizes, usually ranging from 2 mm to 12 mm in diameter. The choice of pellet size is dictated by the intended application’s needs, whether for feeding livestock with specific dietary needs or for producing biomass fuel with optimal combustion characteristics. Ensuring the machine can produce the desired pellet size is pivotal for the intended use case.
By comprehensively evaluating these parameters, users can make informed decisions to select a ring die pellet mill that best aligns with their production goals and operational needs.
Suitable Customers for Ring Die Pellet Mills
The application of ring die pellet machines spans across various industries due to their efficiency and versatility. Understanding the suitable customers for ring die pellet mills allows potential users to evaluate the relevance of this technology in their operational processes. Here, we identify the primary customers who can greatly benefit from employing ring die pellet mills.
1. Agricultural Producers: Farmers and agribusinesses represent a significant segment of users who can leverage ring die pellet machines. These mills are instrumental in pelletizing animal feed, which offers several advantages such as improved feed efficiency, better storage stability, and ease of transport.
By converting raw materials into compact pellets, agricultural producers can optimize feed utilization and potentially enhance the nutritional value of the feed. Additionally, the durability of ring die pellet mills ensures consistent production quality, meeting the high demands of the agricultural sector.
2. Biomass Industry: Companies involved in biomass processing for energy production are another critical customer base for ring die pellet mills. These machines are capable of converting various biomass materials, such as sawdust, straw, and agricultural residues, into high-energy pellets. Biomass pellets serve as an eco-friendly alternative to fossil fuels, providing a renewable energy source.
The ring die pellet mill’s robust construction and high throughput capacity make it ideal for producing large quantities of biomass pellets, thus supporting the growing demand for sustainable energy solutions.
3. Industrial Processors: Various industrial manufacturers utilize pellets in their production processes. For instance, pelletized materials are used in the creation of composites, materials handling, and as a combustion source in industrial boilers.
Industrial processors benefit from ring die pellet mills due to their ability to produce uniform pellets with high density, enhancing the efficiency and consistency of production operations. The capability to handle diverse raw materials further underscores the suitability of ring die pellet mills for industrial purposes.
4. Waste Management Firms: Organizations focusing on waste management can effectively transform waste materials into usable pellets through the application of ring die pellet mills. This includes the conversion of organic waste, municipal solid waste, and industrial by-products into pellets.
The pelletization process not only reduces waste volume but also creates value-added products that can be used as fuel, feedstock, or raw materials for other processes. Waste management firms, therefore, find ring die pellet machines to be a valuable tool in promoting sustainability and circular economy principles.
Why Choose Richi Machinery as a Supplier?
Choosing the right supplier for your ring die pellet machine is pivotal for ensuring efficiency, durability, and high-quality output. Richi Machinery stands out as a leading provider due to several compelling reasons.
Firstly, their commitment to quality assurance is unparalleled. Each ring die pellet mill produced adheres to stringent production standards, ensuring that every machine meets the highest levels of performance and reliability.
Moreover, Richi Machinery prides itself on integrating the latest technological advancements into their products. Their state-of-the-art ring die pellet machines feature innovative technology designed to maximize productivity and efficiency. This commitment to innovation ensures that clients receive cutting-edge equipment that can keep pace with evolving industry demands.
In addition to their superior products, Richi Machinery is renowned for its exceptional customer support. They offer comprehensive support programs designed to assist clients at every stage, from initial inquiry to after-sales service. This strong emphasis on customer service ensures that clients can rely on ongoing technical support and assistance, thereby ensuring seamless operational continuity.
Expanding their influence worldwide, Richi Machinery boasts a robust global reach. Their extensive distribution network ensures timely delivery and local support no matter where clients are located. This global presence demonstrates their capability to effectively serve a diverse, international clientele.
Lastly, Richi Machinery offers comprehensive solutions that span the entire project lifecycle. From the initial design phase to the final installation, they provide a full suite of services tailored to meet specific client needs. This all-encompassing approach ensures that clients have a seamless experience, with every aspect of the process managed by industry experts.
Overall, Richi Machinery’s dedication to quality, technological innovation, customer support, global presence, and comprehensive solutions makes them an ideal supplier for those seeking reliable and efficient ring die pellet mills.
Conclusion
In conclusion, understanding the intricacies of the ring die pellet machine is pivotal for maximizing its benefits and ensuring optimal operation. This machinery, renowned for its efficiency and durability, offers significant advantages including higher productivity, uniform pellet quality, and reduced operational downtime.
Comprehending the working principle of the ring die pellet mill is crucial for anyone involved in feed production or biomass energy generation, as it directly impacts the quality and consistency of the final product.
As we have explored, the suitability of the ring die pellet machine extends across various applications, making it a versatile solution for industries ranging from agriculture to waste management. Its capacity to handle diverse raw materials and produce high-quality pellets consistently underscores its indispensability in modern production processes.
Richi Machinery stands out as a reputable supplier in this field, offering advanced, reliable, and highly efficient ring die pellet machines tailored to meet diverse industrial needs. Their commitment to quality and customer satisfaction makes them a trustworthy partner for your pellet production requirements.
It is advisable for potential users to consult with experts from Richi Machinery to ascertain the best-suited solutions for their specific operational demands.
Exploring the comprehensive applications and benefits of the ring die pellet mill reveals its role as a cornerstone in efficient pellet production. As technologies evolve, staying informed about such machinery ensures your operations remain competitive and sustainable. For those seeking to enhance their production capabilities, the ring die pellet machine is an invaluable asset, and Richi Machinery is well-positioned to support these advancements.